Avanced Ceramics
With over 200 years of expert knowledge and experience in ceramics, Solcera is perfectly placed to fit the most specific requirements for advanced ceramics, also known as technical ceramics.
Assessment of chemical and physical properties of ceramics constitutes an essential step in their manufacture since they will decisively influence their final performances.
Solcera has a considerable range of characterization, analysis, inspection and test equipment, including
- Spectromètre EDX, couplé à un microscope à balayage électronique (MEB) Energy Dispersive X-Ray Spectroscopy (EDS or EDX) coupled to a SEM scanning electron microscopy
- X-ray Diffractometer
- Infrared Spectrometer FTIR
- Density, dilatometer, thermal analyzer, moisture analyzer, rheometer (flow behavior), durometer (Vickers and Knoop hardness), laser granulometer (particle size), BET (surface area analyzer), coulometer
- Mechanical test equipment (biaxial, 3 and 4 points flexural strength, tension, compression, Young’s modulus…)
- Polariscope (stress detection in transparent materials)
- Sample preparation : Precision Cutting, polishing, sputter coating
- Interface analysis
- Electrical testing
- Pressure testing and Helium leak detection
Through this broad expertise, Solcera designs, industrializes and produces ceramics and advanced materials for use in harsh environments.
Our materials are used in the field of civil and military aeronautics, as insulating supports in instrumentation or ballistic protection elements, as well as opto-electronic components in guidance systems.
Solcera is also engaged in metallurgical industries, supplying oxygen sensors and sinter supports as well as in semiconductors and chemistry with their crucibles and labware. Furthermore, we meet regulatory requirements related to nuclear activities. And finally we offer our expertise to luxury jewelry and watchmaking.
Solcera develops its own ceramic grades and is vertically integrated, i.e. owns all steps of the manufacturing process, up to the final ceramic component, with flexible production capacity from prototype to high-volume manufacturing :
- Preparation of powders
- Shaping: uniaxial pressing, isostatic pressing, extrusion, slip casting, injection molding, hot pressing
- Atmosphere and pressure sintering, HIP
- Machining and finishing processes: in the green non-sintered state, in the pre-sintered “bisque” state, grinding, turning, milling, lapping, polishing
Our R&D team is essential for co-development programs with our customers in high-technology markets and we provide product design services and industrial support through our Engineers.
Ceramic manufacturing process
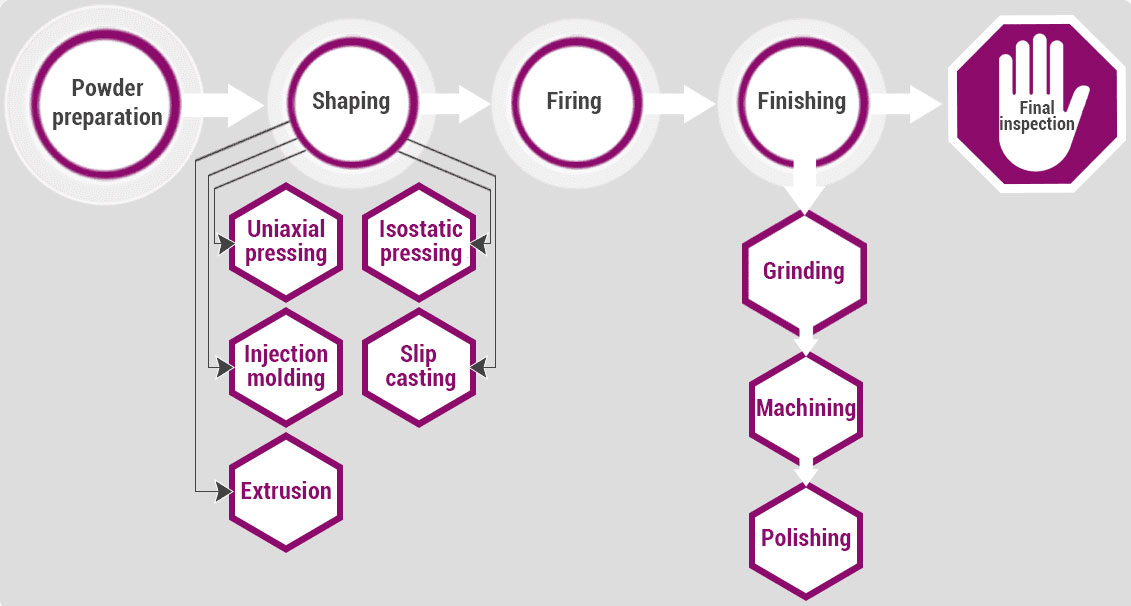
Selection Guide
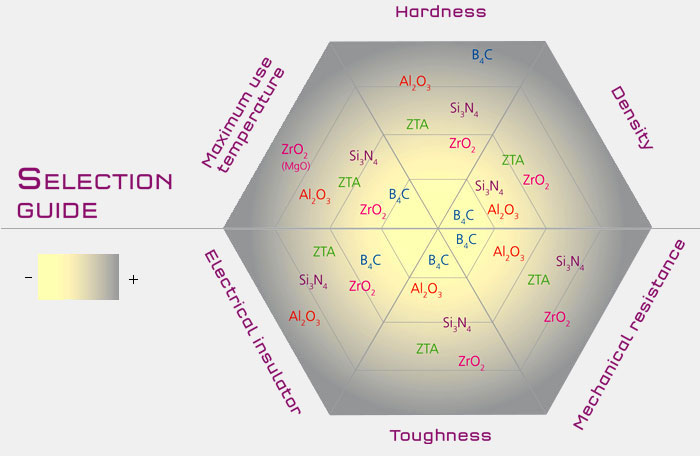
Materials Portfolio
MATERIAL | BENEFITS IN APPLICATION |
---|---|
AI₂0₃ | Hardness, low cost, metallizable |
ZrO₂ (Y₂O₃) | Fracture toughness, bending strength, colors |
ZrO₂ (MgO) | Thermal insulation, mechanical resistance |
ZTA | Fracture toughness, hardness |
SI₃N₄ | Mechanical and wear resistance |
B₄C | Extreme hardness, low density |
MgF₂ | Infrared transparency up to 8μm |
MgAI₂O₄ | Impact and corrosion resistance, transparency |
ZnS | Infrared transparency up to 12μm |
SiO₂ | Electromagnetic transparency |
MgO | Extreme temperature refractory |
HfO₂ | Extreme temperature refractory |
Our materials
Alumina | Zirconia | Nitrides | Boron carbide | Transparent materials | |||||||||
---|---|---|---|---|---|---|---|---|---|---|---|---|---|
Proprerties | Unites | AF950 | TS150 | AF980 | AF997 | ZFME | ZFYT | Kersit | HP B₄C | SiO₂ | MgF₂ | Spinelle | ZnS |
Composition (masse %) | 95% Al₂0₃ | 97,6% Al₂0₃ | 98% Al₂0₃ | 99,7% Al₂0₃ | 97% Zr0₂ | 95% Zr0₂ | 91% Si₃N₄ | 95% B₄C |
99% SiO₂ | > 99,8 % MgF₂ | 100% MgAI₂0₄ | 100% ZnS | |
Density | g/cm³ | 3,60 | 3,75 | 3,89 | 3,89 | 5,70 | 6,00 | 3,20 | 2,50 | 1.9-2.1 | 3,18 | 3,58 | 4,09 |
Hardness - Vickers | GPa | 15 | 15 | 15 | 18 | 11 | 13 | 16 | 28 | 5 | 6 | 13 | 2,9 |
3 points bending strength/ biaxial (b) | MPa | 250 | 280 | 280 | 310 | 600 | 900 | 900 | 425 (4pts) | >40 | 130 | 390 | 95 (b) |
Elastic modulus | GPa | 250 | 330 | 330 | 310 | 210 | 220 | 315 | 440 | 40 | 140 | 270 | 90 |
Fracture toughness | MPa (m)¹/² | 3,8 | 3,8 | 4 | 4,8 | 8,5 | 10 | 7,5 | 3-4 | 2,2 | 0,6 | ||
Coefficient of thermal expansion | 1/K x10⁶ | 8,5 | 8,5 | 8 | 8,5 | 9,5 | 10 | 3,1 | 5 | 0.6 | 10 | 7,8 | 7,3 |
Thermal conductivity (20° à 100°C) |
W/m.K | 22 | 30 | 29 | 1,9 | 3 | 19 | - | 0.9 | 15,3 | 12 | ||
Thermal shocks resistance | +++ | ++ | + | + | ++ | + | +++ | + | ++++ | +++ | + | + | |
Maximum use temperature | °C | 1500 | 1700 | 1500 | 1700 | 2000 | 1000 | 1400 | - | 1200 | 600 | 1500 | 200 |
Electrical resistivity | Ohm.cm | > 10¹² | > 10¹⁴ | > 10¹⁴ | > 10¹² | > 10⁷ | > 10⁷ | > 10¹⁰ | > 10⁷ | > 10⁷ |
This Chart is intended to illustrate typical properties of a selection of Solcera .
Property values may vary with method of manufacture, size and shape of part and may not be used as absolute values.
Avanced Ceramics
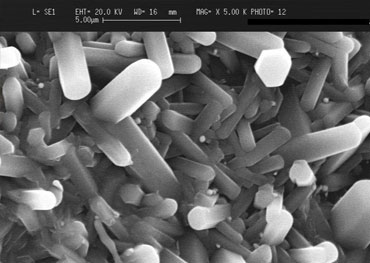
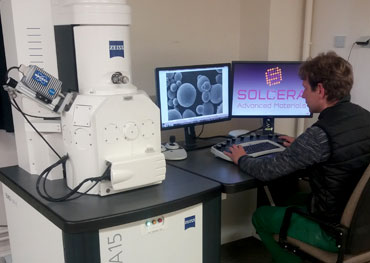
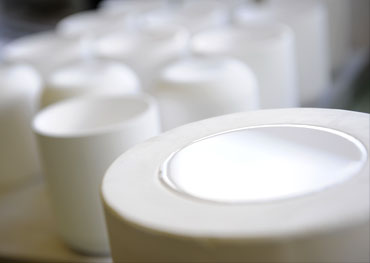
A project, do you need information or advice ?
Read moreContacts
- ZI N°1 - Rue de l'industrie
- 27000 EVREUX
- +33 (0)2 32 29 42 00
- 83 Rue Marcelin Berthelot
- 77550 MOISSY-CRAMAYEL
- +33 (0)1 64 13 61 10
- Contact